What is the Purpose of a Weld Neck Flange?
- sghpipesofficial
- Mar 21
- 5 min read
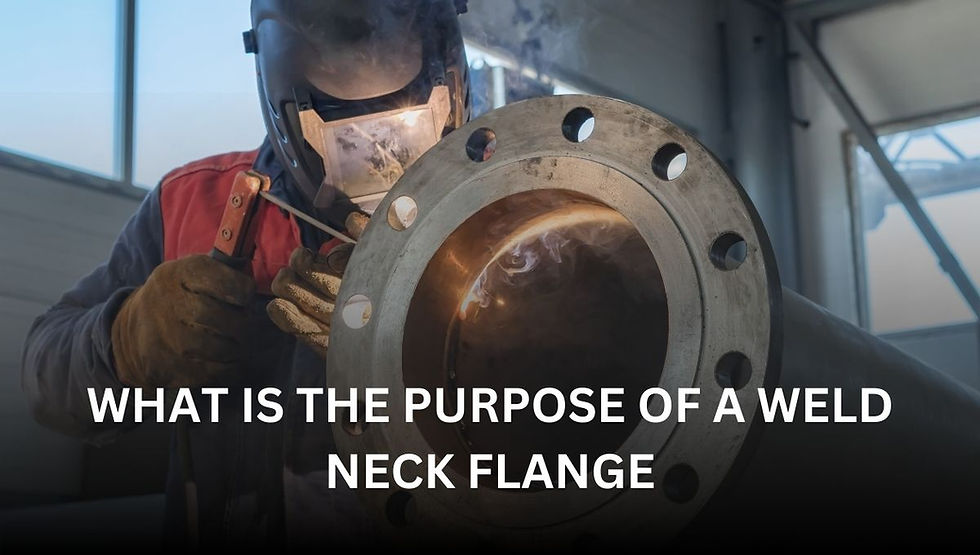
Weld neck flanges play a critical role in industrial piping systems, ensuring durability, strength, and leak-proof connections in high-pressure environments. These flanges are designed for seamless integration, reducing stress concentration and enhancing pipeline integrity. Industries such as oil and gas, power generation, and chemical processing rely on them to handle extreme temperatures and corrosive substances.
Their tapered hub design allows for smooth fluid flow, minimizing turbulence and pressure loss. Unlike other flange types, weld neck flanges provide superior structural integrity, making them the preferred choice for demanding applications. Meeting ASME flange standards, they offer unmatched reliability in critical piping systems. Understanding their function and advantages helps industries make informed decisions for long-term performance and safety.
What is a Weld Neck Flange and How Does It Work?
A weld neck flange is a high-strength pipe fitting designed for high-pressure and high-temperature applications. It features a long tapered hub that distributes stress evenly, reducing the risk of failure in industrial piping systems. This flange is welded directly to the pipe, creating a robust metal joint that enhances pipeline integrity and prevents leaks.
Used in industries like oil and gas, chemical processing, and power generation, weld neck flanges ensure corrosion resistance and durability. Their seamless connection minimizes turbulence and pressure drop, making them ideal for critical piping systems. Built to ASME flange standards, they provide exceptional strength and reliability in extreme environments, making them the preferred choice for high-pressure flange connections and structural stability.
How Does the Design of a Weld Neck Flange Improve Performance?
The design of a weld neck flange enhances performance by ensuring structural integrity, stress distribution, and leak-proof connections in high-pressure systems. Its tapered hub gradually transfers stress from the flange to the pipe, minimizing fatigue and increasing durability. This design reduces turbulence and pressure drop, improving flow efficiency in industrial piping.
Made from stainless steel, carbon steel, or alloy steel, weld neck flanges offer exceptional corrosion resistance, making them ideal for harsh environments. Their full penetration weld ensures a strong, reliable joint that withstands extreme temperatures and mechanical stress. Meeting ASME flange standards, they are widely used in power generation, chemical processing, and gas transmission, where high-pressure applications demand powerful and long-lasting performance.
What Are the Key Advantages of Using Weld Neck Flanges?
Weld neck flanges offer unmatched advantages in industrial piping, making them the preferred choice for high-pressure applications. Their tapered hub design evenly distributes stress, preventing fatigue and enhancing pipeline integrity. The full penetration weld creates a leak-proof joint, ensuring long-term reliability in high-temperature and corrosive environments.
Made from stainless steel, carbon steel, and alloy steel, they provide superior corrosion resistance and durability. These flanges reduce turbulence and pressure drop, improving fluid flow efficiency in power generation, chemical processing, and gas transmission systems. Compliant with ASME flange standards, they offer exceptional mechanical strength and thermal expansion resistance. Their strong construction and seamless integration into piping systems make them essential for safety, performance, and long-term operational efficiency.
Also Read: How to Choose Weld Bends for Pipe System
Where Are Weld Neck Flanges Commonly Used?
Weld neck flanges are widely used in industries requiring high-pressure and high-temperature resistance. In oil and gas pipelines, they ensure leak-proof connections and structural integrity, handling extreme pressure and corrosive substances. Power generation plants rely on these flanges for seamless integration in steam and cooling systems, maintaining efficiency under thermal expansion.
Chemical processing facilities use stainless steel and alloy steel weld neck flanges for corrosion resistance in aggressive environments. In industrial piping for refineries and petrochemical plants, their robust design reduces stress concentration, preventing failures. Meeting ASME flange standards, they are essential for high-pressure applications in shipbuilding, nuclear energy, and heavy machinery, ensuring durability, reliability, and optimal performance in demanding environments.
Many global industries depend on a welding neck flange exporter to source high-quality flanges that meet strict international standards. Whether in gas transmission, food processing, or pharmaceutical manufacturing, businesses rely on trusted exporters to supply durable flanges that ensure long-term operational efficiency.
How Do Weld Neck Flanges Compare to Other Flange Types?
Weld neck flanges outperform other flange types in strength, durability, and pressure-handling capabilities. Unlike slip-on flanges, which rely on fillet welds, weld neck flanges use full penetration welds, ensuring a stronger, leak-proof joint. Compared to socket weld flanges, they provide better stress distribution, reducing the risk of fatigue and failure in high-pressure applications.
Their tapered hub minimizes turbulence and pressure drop, unlike lap joint flanges, which lack a secure fit. While threaded flanges are suitable for low-pressure systems, weld neck flanges excel in industrial piping where structural integrity is critical. Meeting ASME flange standards, they are the preferred choice for power generation, chemical processing, and gas transmission, ensuring long-term performance in extreme environments.
What Are the Best Materials for Weld Neck Flanges?
Selecting the right material for weld neck flanges is crucial for performance, durability, and corrosion resistance in industrial piping. Stainless steel weld neck flanges are ideal for chemical processing and food industries due to their exceptional resistance to corrosive substances. Carbon steel flanges offer high mechanical strength, making them suitable for power generation and gas transmission.
Alloy steel weld neck flanges provide superior performance in high-temperature and high-pressure applications, ensuring structural integrity and thermal expansion resistance. Nickel alloys are preferred for extreme environments, such as offshore drilling, where corrosion and temperature fluctuations are significant concerns. Meeting ASME flange standards, these materials ensure reliability, longevity, and safety in various industrial applications, enhancing pipeline integrity and overall system efficiency.
Also Read: Which Material is Used for Elbows?
How Are Weld Neck Flanges Installed for Maximum Efficiency?
Proper installation of weld neck flanges is essential for ensuring maximum efficiency, leak-proof connections, and long-term pipeline integrity. The process begins with precise alignment of the flange and pipe to prevent stress concentration and misalignment issues. A full penetration butt weld is applied, creating a seamless metal joint that enhances structural strength and prevents leaks in high-pressure applications.
Post-weld inspections, including radiographic and ultrasonic testing, verify weld integrity and compliance with ASME flange standards. Proper torque application on bolts ensures even stress distribution, reducing the risk of flange failure under high temperatures and extreme pressure. Used in power generation, chemical processing, and gas transmission, correctly installed weld neck flanges provide durability, corrosion resistance, and reliable performance in industrial piping systems.
What Are the Pressure Ratings and Standards for Weld Neck Flanges?
Weld neck flanges are designed to withstand high-pressure applications, with pressure ratings classified under ASME flange standards. These ratings range from Class 150 to Class 2500, indicating their ability to handle varying pressure and temperature conditions.
Higher-rated flanges, such as Class 1500 and above, are used in power generation, chemical processing, and gas transmission, where extreme conditions require superior strength. A reliable welding neck flange exporter ensures that all products meet ASME B16.5 and B16.47 standards, providing industries with high-quality, high-pressure solutions.
The strong design ensures even stress distribution, reducing the risk of fatigue and failure. Compliance with ASME B16.5 and B16.47 standards guarantees structural integrity, corrosion resistance, and safety in industrial piping. Selecting the right pressure rating ensures long-term durability and reliability, making weld neck flanges essential for high-pressure and high-temperature environments.
Conclusion
Weld neck flanges are the ideal choice for industrial piping systems requiring durability, strength, and leak-proof performance. Their tapered hub design ensures even stress distribution, reducing the risk of failure under high-pressure and high-temperature conditions. Used in power generation, gas transmission, and chemical processing, they provide superior structural integrity and corrosion resistance.
Meeting ASME flange standards, these flanges offer reliability in demanding environments where safety and efficiency are critical. Unlike other flange types, their full penetration weld enhances joint strength, minimizing pressure drop and turbulence. Choosing weld neck flanges guarantees long-term performance, making them a preferred solution for industries that prioritize pipeline integrity, high-pressure applications, and overall system reliability.
Comments