What is the Purpose of the Side Bend Test in Welding | Ultimate Guide 2025
- sghpipesofficial
- Feb 20
- 5 min read
Updated: Jun 27
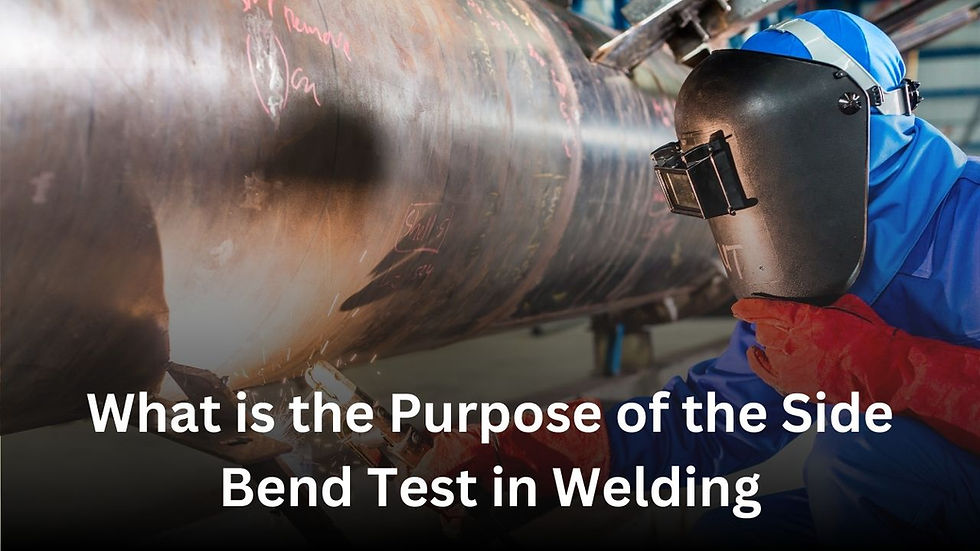
Did you know that even the strongest-looking welds can have hidden defects that compromise structural integrity? In industries like construction and manufacturing, ensuring weld durability is crucial to prevent costly failures and safety risks. That’s where the side weld bends test comes in.
This essential test exposes internal flaws that could weaken a weld under stress. If you're a welder, inspector, or engineer looking to improve weld quality, knowing about what is the purpose of the side bend test in welding is key. This article will explain how the test works, its importance, and how it helps meet industry standards.
By the end, you'll know how to analyze weld strength effectively and ensure compliance with essential welding codes.
Overview of the Side Bend Test in Welding
Aspect | Details |
Definition | A mechanical test used to evaluate the ductility and internal soundness of a welded joint. |
Purpose | To detect internal defects and ensure the weld can withstand bending stress without cracking. |
Common Use Cases | Welder performance qualification, procedure qualification, structural testing in construction, shipbuilding, pipelines. |
Applicable Standards | AWS D1.1, ASME Section IX |
Specimen Orientation | Cut perpendicular to the weld and bent sideways to expose full weld thickness. |
What is a Side Bend Test?
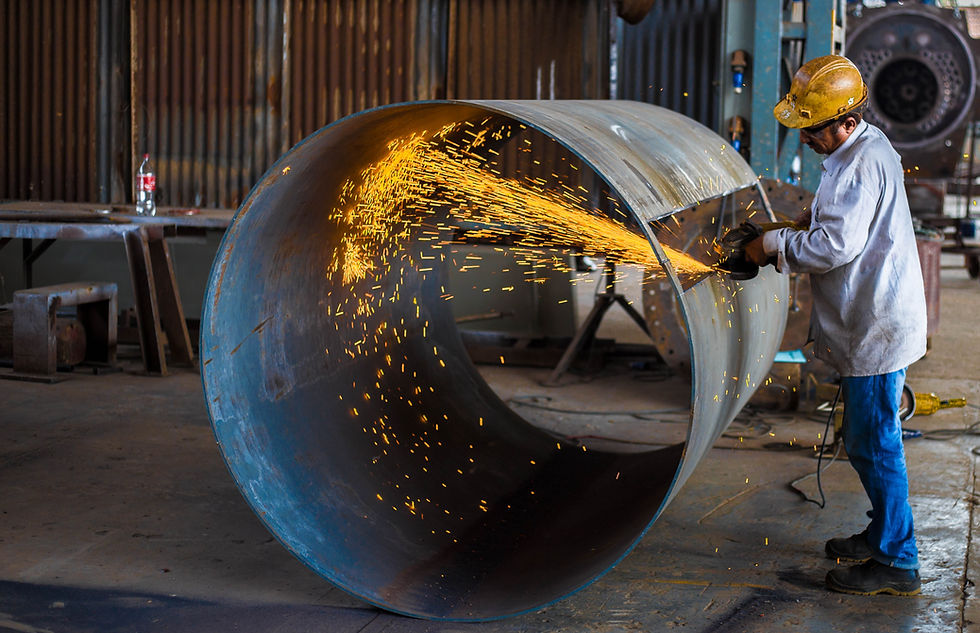
The side bend test is a mechanical testing method used to judge the ductility and soundness of a weld by bending the sample at a specific angle. The specimen is extracted from the welded joint and placed under a weld bend test mandrel, forcing it to bend in a way that exposes internal defects.
Unlike the face side and root side bend tests, which assess individual sections, the side bend test covers the entire weld thickness, making it more effective for thicker materials. It is commonly used in welder performance qualification and procedure qualification to ensure compliance with industry standards such as AWS D1.1 and ASME Section IX.
Understanding bend test welding is essential for ensuring structural integrity, as it helps detect potential weaknesses that could lead to weld failures. The welding bend test is a critical method for determining a weld’s ductility and detecting internal defects that might not be visible externally.
What are the Types of Bend Test in Welding
Bend tests in welding are essential for measuring a weld’s ductility, strength, and flaw resistance. There are several types of bend test in welding, including the side bend test, face bend test, root bend test, transverse bend test, free bend test, flattening test, and guided bend test. Each method serves a distinct purpose, such as assessing weld penetration, fusion, and overall joint integrity.
The side bend test welding method examines weld toughness by bending the specimen perpendicular to the weld axis, while the transverse bend test evaluates tensile strength across the weld. Additionally, pipe weld bend testing ensures the flexibility and durability of pipeline welds under stress.
These tests are essential for bend testing of welds in structural, industrial, and pipeline applications, helping maintain welding quality standards and compliance.
What is the Purpose of the Side Bend Test
The primary objective of the side bend test is to assess the structural integrity in welding. It ensures that the weld metal and base metal are properly fused and can withstand bending stress without cracking. If a weld lacks sufficient ductility, it may fail under operational loads, leading to serious safety risks.
The test also helps identify welding defects such as incomplete fusion, slag inclusions, and cracks, which can compromise the weld’s strength. This testing method is particularly valuable for weld overlay PQR and groove weld PQR, where consistency and defect-free performance are mandatory.
The purpose of bend test in welding is to assess the weld’s ductility and identify any hidden defects that could compromise structural integrity.
When is the Side Bend Test Applied?

This test is typically used for thicker welding test coupons, especially those exceeding 12mm in thickness. It is preferred over longitudinal bend tests and transverse tests when a full-depth assessment of the weld joint is required. Industries such as pipeline construction, shipbuilding, and heavy machinery manufacturing rely on this test to verify weld durability.
It is also essential to review dissimilar materials and similar materials to determine their compatibility under stress. Ensuring that welds meet the necessary welding performance evaluation criteria prevents failures in high-pressure applications.
While the side bend test is highly effective in identifying internal flaws, improper execution or poor weld quality can lead to weld bend test failures, making it essential to follow correct testing procedures. The side bend weld test is widely used to check weld penetration and fusion by revealing internal discontinuities.
Also Read: How to Choose Weld Bends for Pipe System
Procedure for Conducting a Side Bend Test
To perform the test, a test coupon is cut from the welded plate perpendicular to the weld’s longitudinal axis. The specimen is prepared according to industry standards, ensuring it has the correct width and thickness.
During testing, it is placed in a guided bend test fixture where force is applied to bend it around a specific bend test mandrel until it reaches the required angle. The original gauge length and gauge lines are monitored to measure deformation and identify defects.
If the weld sustains bending without cracks larger than the allowable limit, it passes. If cracks appear beyond the acceptable threshold, the weld fails, indicating the need for process adjustments.
The side bend test specimen is cut from the welded joint, ensuring it represents the weld’s overall quality before being subjected to bending.
Standards and Codes Governing Side Bend Tests
Regulatory bodies such as the American Welding Society (AWS) and the American Society of Mechanical Engineers (ASME) have established guidelines to standardize the side bend test procedure.
Compliance with AWS D1.1 and ASME Section IX ensures that welds meet safety and performance standards. These codes specify the test longitudinal bend test material, initial bend angle, and acceptable defect limits. Meeting these requirements is necessary for welding joint testing and certifying welders for industrial projects.
In addition to the standard side bend test, the transverse side bend test is often used to evaluate weld ductility and overall performance under stress.
Advantages of the Side Bend Test
This test provides a thorough assessment of a weld’s quality by revealing internal defects that other common welding test procedures might miss. It is cost-effective and straightforward, making it ideal for non-destructive testing for welds.
Unlike tensile test procedures and hardness tests, which require complex equipment, the side bend test offers a direct evaluation of welding test methods with minimal setup. It also helps in verifying wholesale welding bend manufacturers' product quality, ensuring that their materials meet industry standards.
Using the right weld bend test fixture ensures accurate results as it properly supports the test specimen and applies uniform force during bending.
Limitations and Considerations
While the side bend test is highly effective, it has limitations. Improper test coupon preparation can introduce artificial defects, leading to inaccurate results. The test is also limited in detecting root material properties that may affect long-term performance.
Additionally, different materials react differently to bending forces, requiring adjustments in test parameters for accurate assessments. To ensure reliability, proper weld inspection techniques should be followed in conjunction with other important tests, such as free bend tests and transverse tests.
Conclusion
The side weld bend test is an essential tool for evaluating weld strength and integrity. Assessing the mechanical properties of the weld helps ensure that structures remain safe and reliable.
Compliance with industry standards and careful execution of the test can prevent costly failures and enhance welding quality assurance. Whether in structural fabrication, pipeline installation, or heavy equipment manufacturing, this test remains a key component of testing welded joints and maintaining high-quality standards in welding operations.
Comments